Global supply chain issues are having a huge impact on a number of industries, particularly when it comes to sourcing electronics components. In the defence industry, parts shortages are affecting programme delivery and there are unwanted delays as a consequence. In this blog, we explore the need for robust supply chain management and how GRiD can mitigate risk as an OEM of rugged computers.
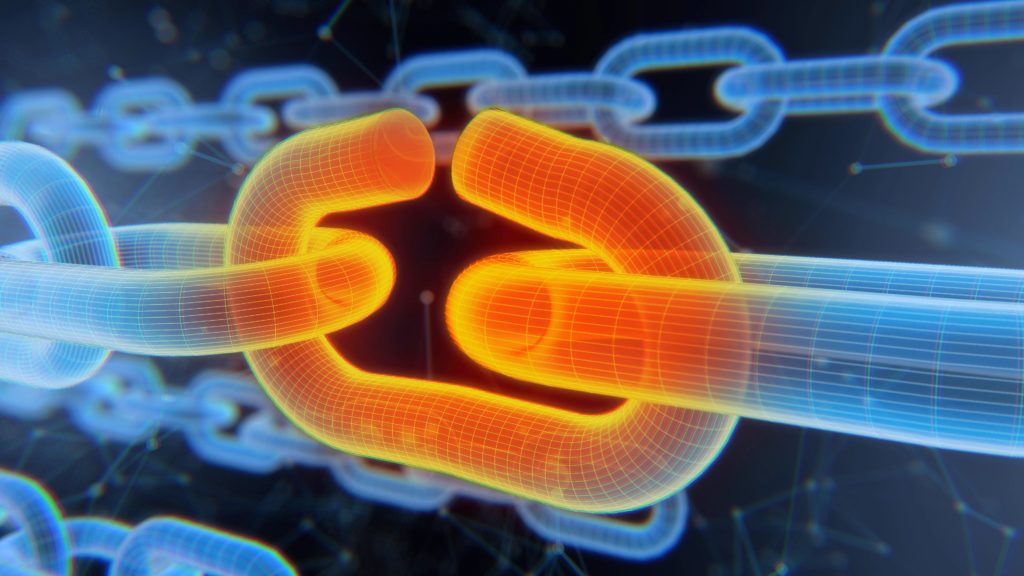
Virtually every equipment manufacturing company in the defence sector, and countless more outside, will tell you the same thing; they will say that their biggest headache in the current climate is maintaining a robust supply chain. It has become a massive problem for all, and it’s not likely to go away any time soon.
The current supply chain problems have resulted from a number of factors that have combined to form a “perfect storm” that has blighted industries from automobiles, to mobile phones and computing devices, to defence programmes large and small. The end result has been a series of delivery slippages and rising costs. No-one really knows when the current situation will change for the better, but most agree that it will last for many months, maybe years.
What is causing the current supply chain issues?
There are a number of reasons from international tariffs to shortages of transportation, as well as the effects of the war in Ukraine. By far the biggest factor, however, is the COVID pandemic and the staff shortages that have gone with it. The initial round of lockdowns meant that many workers were laid off, and since businesses re-opened, it has been difficult to recruit personnel.
For the electronics industry in particular, the wide-reaching lockdowns that continue to be imposed in the Far East are seriously affecting the supply of crucial components, such as processing chips and printed circuit boards (PCBs). Heightening tensions over Taiwan may yet exacerbate the situation.
A solution is not as simple as just building more fabrication plants, as these require huge investment and it takes years for them to become productive. By the time that they are ready to deliver, the current spike in demand may no longer exist.
In terms of major defence programmes, most of the supply problems occur in the lower tiers of the production chain, but they can have an effect out of all proportion to their nature. Delays in sourcing a small component may prevent a company from supplying electronic equipment that, in turn, prevents a second-tier systems integrator from supplying a communications system, for example, to the prime contractor.
The inability to acquire a small item in a timely fashion can ultimately lead to delays in delivering a complete combat system, such as a tank or a helicopter, which has follow on consequences for the capability of frontline troops.
Being in control of supply chain management
In response to the supply chain crisis, many companies are attempting to source the required components from alternative sources, effectively creating a new market that has flourished in recent times as a result of the issues described above. A number of suppliers have made good businesses out of buying up rare and desirable components for resale.
However, these naturally come at an elevated price, but paying the extra may be the optimum way of making sure that delivery promises are met. If this route is used, it has been important to use suppliers who apply their own quality control tests and guarantee that their components are genuine and authentic, perform, and conform, to required standards.
GRiD Defence Systems is one of the many companies feeling the pressure of supplies, but compared with other companies in the same market space it has a unique edge that allows it to stay on top of supply issues.
While its competitors are largely re-sellers of imported equipment, GRiD has the significant benefit of being an original equipment manufacturer (OEM)—it makes its own products and is therefore in complete control of its own supply chain. As an OEM, GRiD has Full Configuration Control of its portfolio, which gives it the key ability to redesign its products to consider the availability, or otherwise, of electronic components.
This opens up a number of options to maintain timely deliveries of products.
Redesigning complex parts in-house
For a start, GRiD can redesign a rugged laptop or tablet to accommodate a different, available component that performs the same task, so that the required product performance is maintained. A more radical answer could be to redesign—or “re-spin”—the PCB itself, to accommodate new chips. This can be a time-consuming process, but GRiD is unique in its market space in having the innate expertise to undertake this complex task.
Another option is to find a form/fit/function “like-for-like” replacement for hard-to-get components from a different supplier. This, however, is likely to require re-qualification of the product, which can get costly, but again it may be worth the expense in order to keep deliveries flowing.
Read more: How to manage electronics obsolescence in military equipment
To augment these solutions GRiD continues to apply other supply chain management best practices. Maintaining a close relationship with suppliers is key here, ensuring that GRiD is the first to know of impending issues while the supplier is aware of upcoming requirements at an early stage. To that end the company has engaged local suppliers where possible to keep lines of communication short, and maintain personal contacts with them on a regular basis.
Another practice that mitigates supply problems is the stockpiling and long-lead procurement of crucial components. This requires regular coordination between sales, procurement and production departments to forecast which components are likely to be needed in the future, and conversely to avoid money being unnecessarily spent on components that may never be required.
Only a company with the high level of in-house experience and expertise that GRiD possesses can fully leverage these options to overcome this industry-wide problem. The supply chain crisis is complex and is likely to continue for the foreseeable future, so it is important to work with a supplier such as GRiD that understands how to mitigate the risk created by this uncertain environment.
Want to learn more about best practices for supply chain management? Contact us if you require further assistance and our expert team can advise on +44 (0)1628 810 230 or drop an email to sales@griduk.com